The concept of "M Build" has been gaining traction in recent years, captivating the attention of developers, architects, and tech enthusiasts alike. The term "M Build" refers to a cutting-edge approach in the construction and technology industries, focusing on modular and sustainable building practices. This innovative method not only revolutionizes the way we create spaces but also enhances efficiency, cost-effectiveness, and environmental responsibility. As urbanization continues to accelerate, the demand for sustainable and efficient building solutions like "M Build" is becoming increasingly vital.
As the world embraces the digital age, the integration of technology into construction processes has never been more crucial. "M Build" leverages advanced technologies such as Building Information Modeling (BIM), 3D printing, and Internet of Things (IoT) to streamline the construction process. These technologies enable precise planning, real-time monitoring, and seamless project management, ensuring that every aspect of a building's lifecycle is optimized for performance and sustainability. The result is a harmonious blend of innovation and practicality that meets the demands of modern living.
With the growing awareness of environmental challenges, "M Build" offers an eco-friendly solution that aligns with global sustainability goals. By utilizing prefabricated components and minimizing waste, this approach significantly reduces the carbon footprint of construction projects. Additionally, "M Build" promotes energy efficiency by incorporating smart systems that optimize resource consumption. Whether it's residential, commercial, or industrial projects, "M Build" is set to redefine the future of construction, making it a compelling choice for stakeholders committed to creating a better world.
Table of Contents
- What is M Build?
- How Does M Build Work?
- Benefits of M Build
- Challenges in M Build
- M Build Technologies
- How Does M Build Promote Sustainability?
- What Are the Cost Advantages of M Build?
- M Build in Residential Projects
- M Build in Commercial Projects
- Can M Build Reduce Construction Time?
- Future Trends in M Build
- Case Studies of Successful M Build Projects
- How to Get Started with M Build?
- M Build and Regulatory Compliance
- M Build vs. Traditional Construction Methods
What is M Build?
The term "M Build" stands for Modular Build, a construction technique that emphasizes the use of prefabricated sections or modules. These modules are manufactured in a controlled factory environment and then transported to the construction site for assembly. This method contrasts with traditional construction, where all building activities occur on-site. The modular approach allows for greater precision, reduced construction time, and minimized waste, making it an attractive option for various types of projects.
How Does M Build Work?
The process of M Build begins with detailed planning and design, often using advanced software like Building Information Modeling (BIM). Once the design is finalized, modules are constructed in a factory setting, where factors like weather and site conditions do not interfere with the timeline. Each module is crafted to exact specifications, ensuring that they fit together perfectly once they reach the construction site. The on-site assembly is comparable to piecing together a puzzle, which significantly speeds up the overall construction process.
Benefits of M Build
M Build offers numerous advantages over traditional construction methods. Some of the key benefits include:
- Reduced construction time: Prefabrication allows for simultaneous site work and module construction, cutting down the overall timeline.
- Cost-effectiveness: Factory production lines are more efficient, reducing labor costs and material waste.
- Quality control: Controlled environments ensure higher quality and precision in construction.
- Eco-friendliness: Minimizes waste and promotes energy efficiency, aligning with sustainable building practices.
Challenges in M Build
While M Build offers numerous benefits, it also faces certain challenges. These include:
- Logistical complexities: Transporting large modules to the site requires careful planning and coordination.
- Initial costs: The upfront investment for modular construction may be higher, although it is offset by long-term savings.
- Regulatory hurdles: Navigating building codes and zoning regulations can pose challenges for modular projects.
M Build Technologies
M Build is supported by a range of innovative technologies that enhance its effectiveness:
- Building Information Modeling (BIM): Facilitates precise planning and coordination among stakeholders.
- 3D Printing: Allows for the creation of customized components and reduces material waste.
- Internet of Things (IoT): Integrates smart systems for real-time monitoring and energy management.
How Does M Build Promote Sustainability?
Sustainability is at the core of the M Build philosophy. By producing modules in a controlled environment, waste is significantly reduced. Additionally, the modular approach often incorporates sustainable materials and energy-efficient systems, further reducing the environmental impact. Smart technologies integrated into M Build projects enable efficient resource management, contributing to long-term sustainability goals.
What Are the Cost Advantages of M Build?
While the initial costs of M Build may be higher due to factory setup and technology investment, the long-term savings are substantial. The efficiency of prefabrication reduces labor costs and minimizes material waste, leading to lower overall project expenses. Moreover, the speed of construction reduces financial outlays related to project delays and prolonged site operations.
M Build in Residential Projects
The residential sector has embraced M Build for its ability to deliver high-quality homes in a fraction of the time required by traditional methods. Modular homes offer flexibility in design and can be tailored to meet the specific needs of homeowners. The speed and cost-effectiveness of M Build make it particularly appealing for affordable housing initiatives, where rapid deployment is essential.
M Build in Commercial Projects
Commercial projects benefit greatly from the efficiencies offered by M Build. Office buildings, hotels, and retail spaces can be constructed faster and with fewer disruptions to surrounding areas. The precision of factory-built modules ensures high standards of quality and safety, which are crucial in commercial settings. Additionally, the adaptability of modular designs allows businesses to expand or modify their spaces as needed.
Can M Build Reduce Construction Time?
Yes, one of the most significant advantages of M Build is its ability to drastically reduce construction time. By manufacturing modules in a factory while site preparation occurs simultaneously, the overall timeline is compressed. This parallel processing means projects can be completed in nearly half the time of traditional construction, offering a competitive edge in fast-paced markets.
Future Trends in M Build
The future of M Build is promising, with several trends emerging that will further enhance its impact:
- Advanced robotics and automation: Increasing precision and efficiency in module production.
- Integration with renewable energy: Incorporating solar panels and energy storage solutions into modular designs.
- Smart city initiatives: Using modular construction to rapidly expand urban infrastructure.
Case Studies of Successful M Build Projects
Examining successful M Build projects provides valuable insights into its potential. Examples include:
- The construction of modular hospitals during health emergencies, showcasing rapid deployment capabilities.
- Large-scale residential developments in urban areas, demonstrating cost and time savings.
- Commercial complexes that leverage modular flexibility for adaptive re-use and expansion.
How to Get Started with M Build?
For those interested in implementing M Build, the following steps can serve as a guide:
- Research and select experienced modular construction firms.
- Engage with architects and engineers to develop a modular-friendly design.
- Consider logistics and transportation needs for module delivery.
- Ensure compliance with local building codes and regulations.
- Utilize technology for project management and monitoring throughout the construction process.
M Build and Regulatory Compliance
Navigating the regulatory landscape is essential for the success of any M Build project. Stakeholders must work closely with local authorities to ensure that modular designs meet building codes and zoning requirements. Understanding and adhering to these regulations from the outset can prevent costly delays and facilitate smoother project execution.
M Build vs. Traditional Construction Methods
Comparing M Build to traditional construction highlights the transformative potential of modular techniques. While traditional methods rely heavily on on-site labor and are susceptible to weather-related delays, M Build offers a level of precision and efficiency that is unmatched. The ability to deliver high-quality structures quickly and sustainably makes M Build a compelling alternative that addresses the limitations of conventional construction.
You Might Also Like
The Enchanting World Of Bijou PoodlesDiscover The Exceptional Services Of J & J Truck Wash & Repair
Discover The Ultimate Experience At Love Nails & Spa Inc
Peerless Potato Chips: A Crunchy Legacy In Gary, Indiana
Unlocking The Potential Of "M Build": A Comprehensive Guide
Article Recommendations
- Discover The Love Story Of Jared And Pandora A Journey Of Hearts
- Cynthia Erivos Triumph At The Kennedy Center Honors
- Amazing Cliff Richard Tshirts Show Your Love For The Music Legend
- Discover The Ultimate Big Star Band Shirt Elevate Your Style
- Read The Epic Conclusion Captain Underpants And The Preposterous Panty Plot Book 12
- Marvelous Renata Friedman Unlocking The Secrets Of Insert Suffix
- Tim Buckleys Net Worth A Detailed Look At His Wealth And Legacy
- Discover Jessica Simpsons Stunning Maxi Dresses
- Unveiling The Net Worth Of Legendary Irish Rockers How Much Is U2 Worth Today
- How Much Money Does Jeff Bezos Make Per Second Unveiled
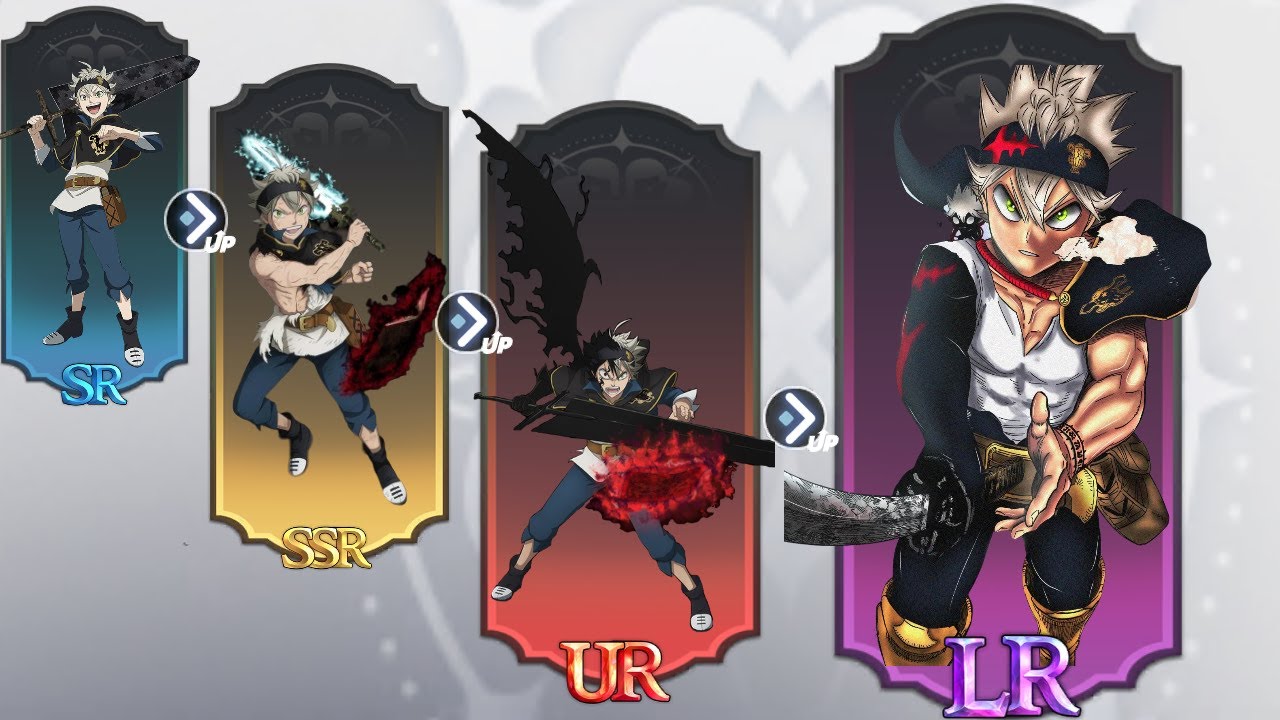